How Can Our Vector Range Optimise Your Turbocharger Impeller Process?
Faster Turbocharger Impeller Grinding (Profile and Groove):
CMT engineers have extensive experience and knowledge of vane grinding through direct involvement on bespoke customer projects. We will offer our professional opinion on what is practically achievable with your vane specifications.
For turbocharger impeller grinding, the workpiece is made from a high temperature resistance alloy which makes it difficult to grind. CMT are experts at customising this precision grinding process to suit your needs.
The high rigidity of the Vector spindle makes fast metal removal rates possible. For medium volume production, the Vector Basic with conventional abrasive wheels can be used to plunge grind the groove and form together. For higher volumes, the Vector Twin with super abrasive wheels gives optimum spindle utilisation.
CMT has also created a fully autonomous system for grinding the turbocharger shaft and wheel assembly, specifically the impeller profile and oil seal grooves. This offers you faster production times.
Turbocharger Shaft and Wheel – Customisation as Standard
There are many options for your turbocharger production machine’s final engineered solution. Parts handling may be via multi-position pallets, single part pallets with through conveyor, or linear transfer without pallets. Options may include post process gauging and post process de-burring, along with various feature detection systems.
CMT will guide you to assess the benefits of these options, along with type of grinding wheel and coolant used, for instance vitrified CBN or conventional along with either emulsion or neat oil coolant. We can also advise whether dressing of the wheel should be done with either a diamond roll or a diamond disc.
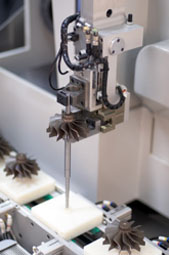
CMT can create a flexible loading system to enable a wide range of different size turbocharger components to be processed.
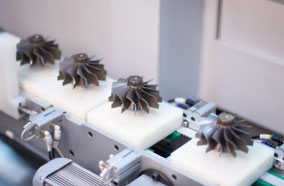
This single part feeding system allows you to cater for a range of different size turbocharger components.
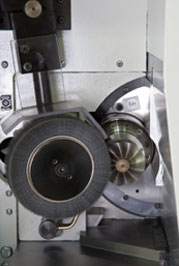
The ancillary deburring process enables component deburr post grinding and prior to unloading from the machine.
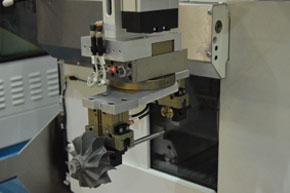
CMT has designed this turbocharger load – turnaround – unload system to give a faster part exchange rate.
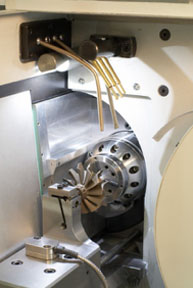
A turbocharger clamped in position ready for profile grinding using a tail stock support to facilitate shortest possible grinding cycle time, using the latest “gap and crash” sensor technology.
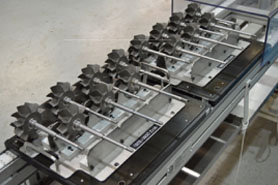
This turbocharger pallet feeding system enables optimised processes for the same sized parts.
Please contact us for enquiries.